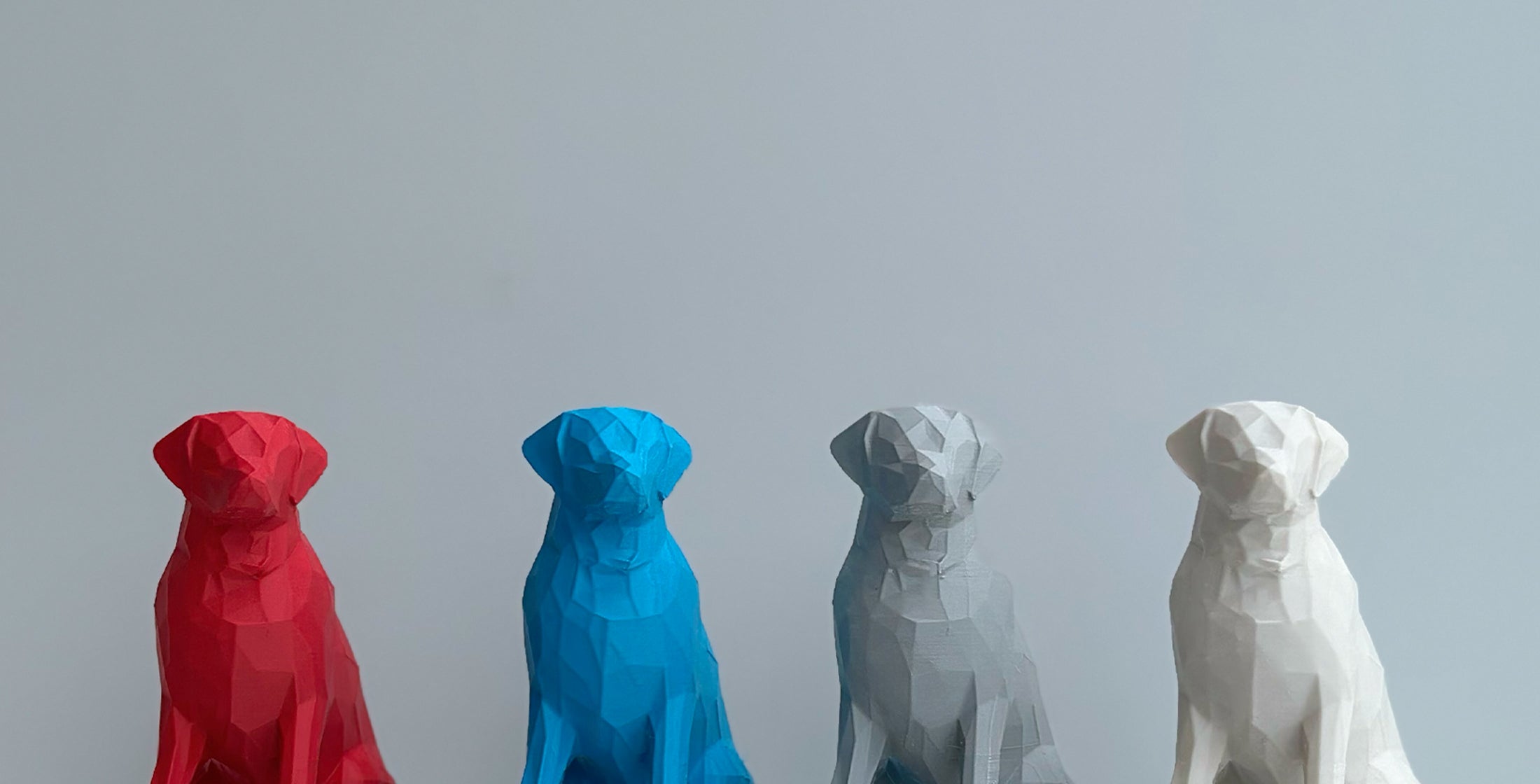
GREENER PRINTS, BIGGER IMPACT
WHY FILACORP?
At Filacorp, we believe that sustainability is key, we wish this to be the first choice for all creators using 3D printing. We make it easy for you to make that choice, with no inflated costs along with no compromises towards the quality of your creations.
Our materials are gathered with the highest quality in mind, in collaboration with leading recyclers and their discarded plastic. With years of perfecting our process, we're excited to see you use our flagship materials to bring your creations to life.
-
RESPONSIBLE RECYCLING
We'll make sure all the plastic waste is tackled while you can focus on creating classy, high-quality work
-
QUALITY MATTERS
With performance testing, our recycled material is pushed to their limit to produce products that are reliable, functional, and durable
-
OPTIMAL RESULTS
We go above and beyond to ensure cross-compatibility with our materials while offering you with all the help you need
Your Plastic's Journey
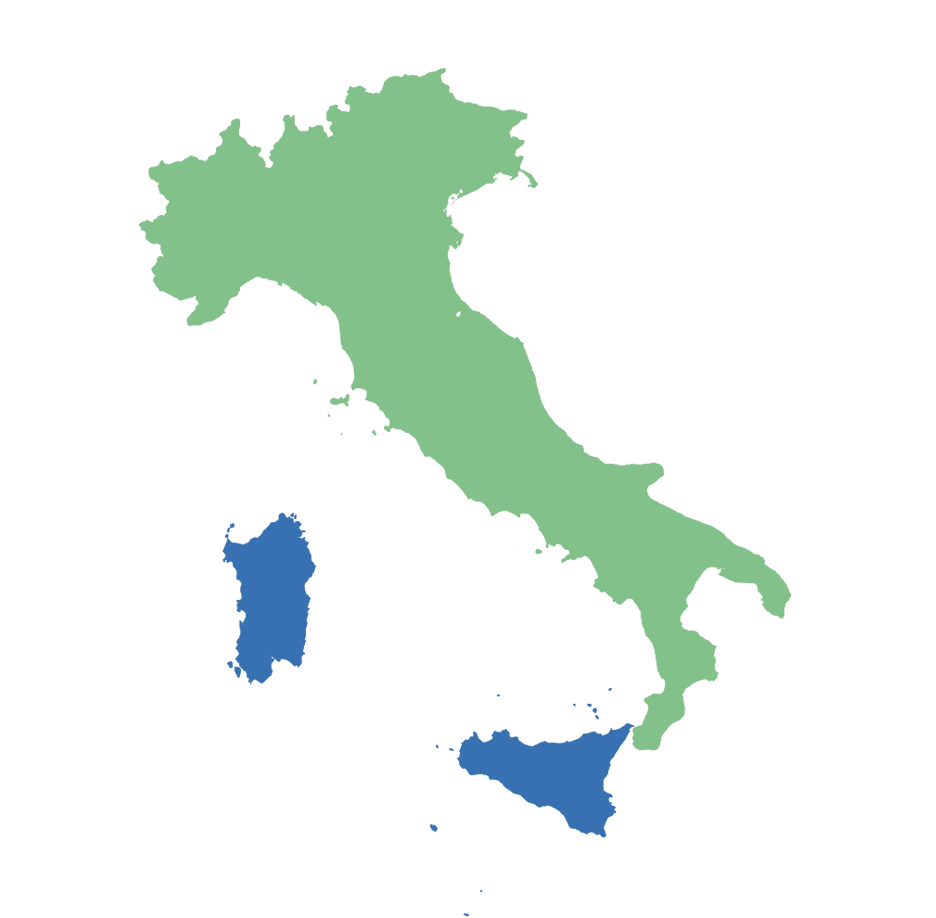
Raw Materials
Transforming Waste into Innovation
Our plastic is gathered and reprocessed in Italy. Starting as unwanted industrial waste, various PLA items were carefully collected and Recycled, Reshaping them into the eco-friendly product you can use to Reprint your ideas into reality
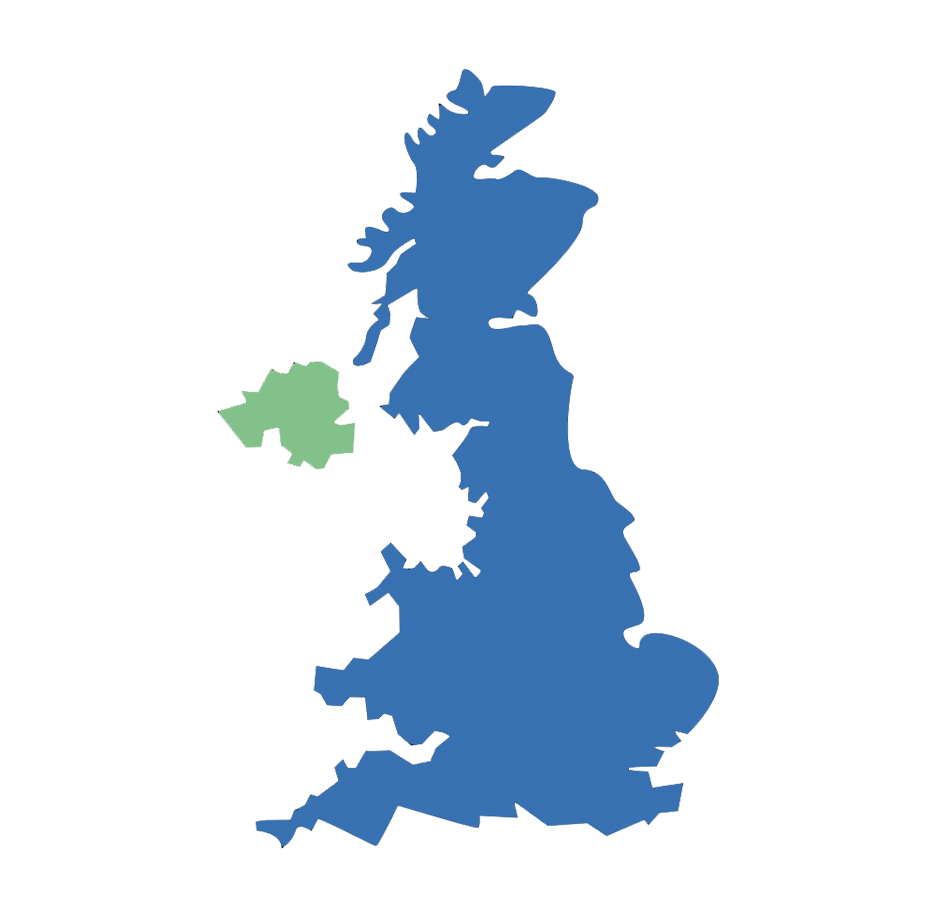
Colourant
Colourful Beginnings
Our environmentally friendly colours are sourced from the United Kingdom. The coloured pigments are sustainably created, using 100% Green Energy. These additives are then mixed in with our recycled PLA Pellets to create the vivid colour found in your filament
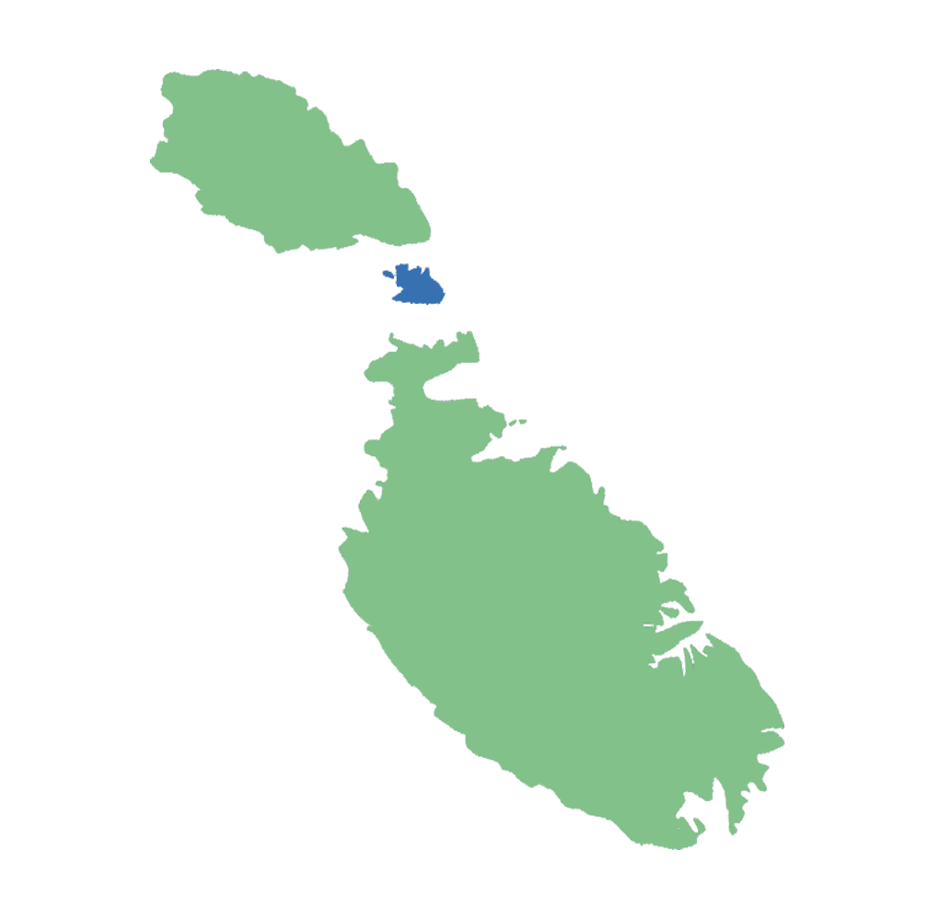
Manufacturing
Crafted Locally with Care
Our last step is transforming the high-quality recycled materials into our sustainable filament line-up, which is proudly manufactured in Malta. Using advanced technology, we extrude them into 3D printing filaments while maintaining strict quality control standards
Our Step-By-Step Manufacturing Process
-
STEP 1 - DEHYDRATION
The recycled raw material is dehydrated to remove moisture, ensuring optimal filament quality
-
STEP 2 - COLOUR PREPARATION
Precise colorants are measured and mixed to achieve the exact shade and consistency
-
STEP 3 - EXTRUSION
The material is melted and extruded into a continuous, smooth filament ready for further processing
-
STEP 4 - COOLING & DRYING
The newly extruded filament is carefully cooled in a water bath, which stabilises its shape. It is then dried to remove any residual water particles
-
STEP 5 - LASER MEASURING
As the filament exits cooling, lasers continuously monitor its diameter. This ensures every spool meets exacting standards for accuracy and consistency.
-
STEP 6 - WINDING & PACKAGING
The finished filament is tightly wound onto spools, carefully inspected, vacuum packaged for delivery
WHY RECYCLED MATERIALS?
Although other companies use standard virgin plastic, we decided to be different. With the growing plastic pollution problem, we aim to reduce past, present and future waste by combining recycling and the growing 3D printing industry
-
Environmental Benefits
You can help reduce the amount of plastic waste in landfills and oceans while also promoting a more sustainabe future for eveyone
-
rPlastic Quality
rPLA filaments have the same strength and flexibility as non-recycled filaments, while also being more sustainable
-
Durability
Just as durable, 100% more sustainable. They have high impact resistance making them ideal for use in functional parts and prototypes
-
Recycled Strength
The strength properties are close to identical when compared to traditional counterparts, but with the added benefit of being more sustainable
-
Temperature Resistance
Recycled filaments have similar temperature resistance when compared to their non-recycled counterparts
-
Printing Odour
rFilaments produce less odour, making them a better choice for use in enclosed spaces. This can making 3D printing more healthy experience
Don't Believe us? Have a look for yourself
Both printed on the Creality Ender 3 S1 Pro with the same settings
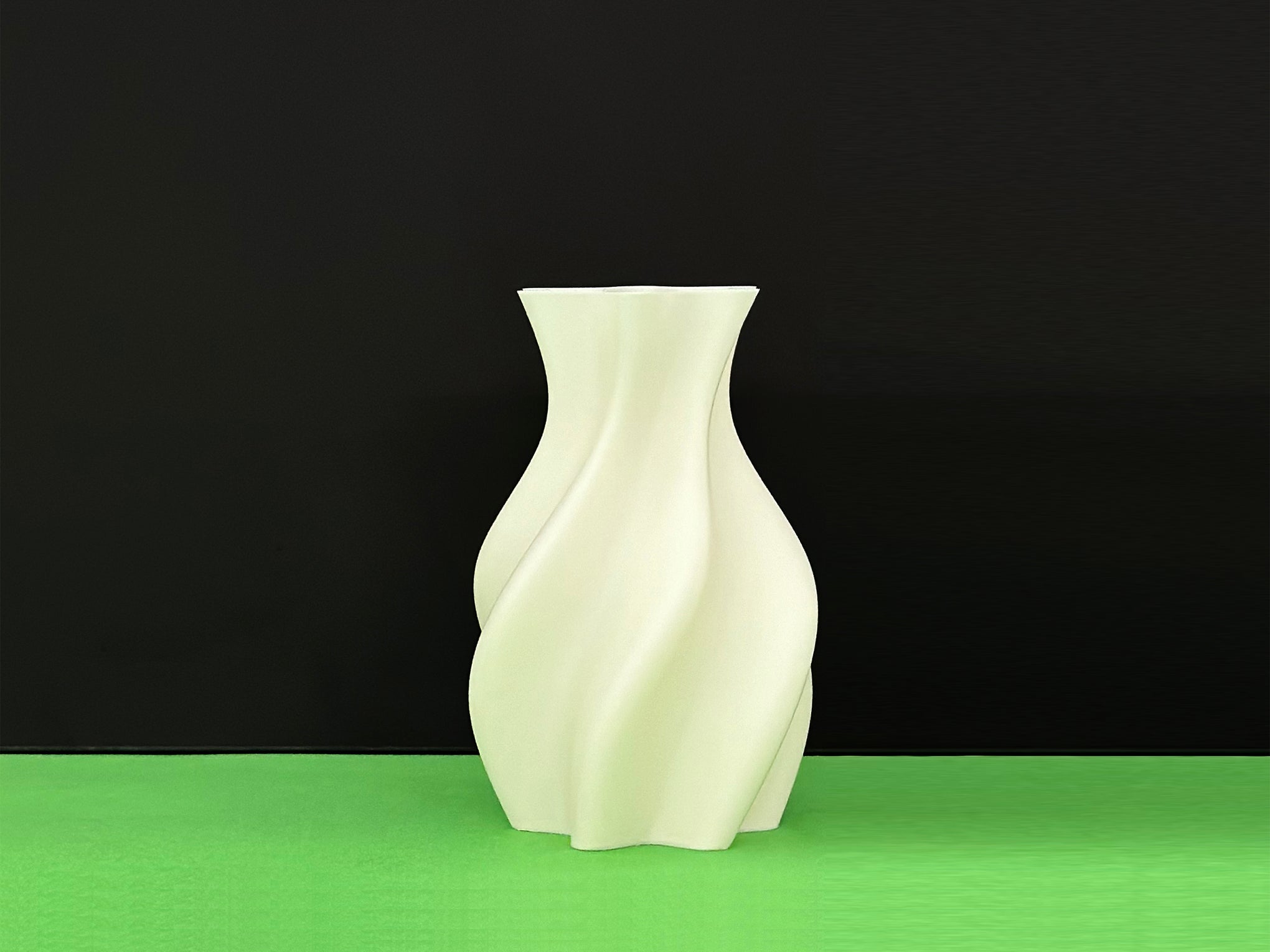
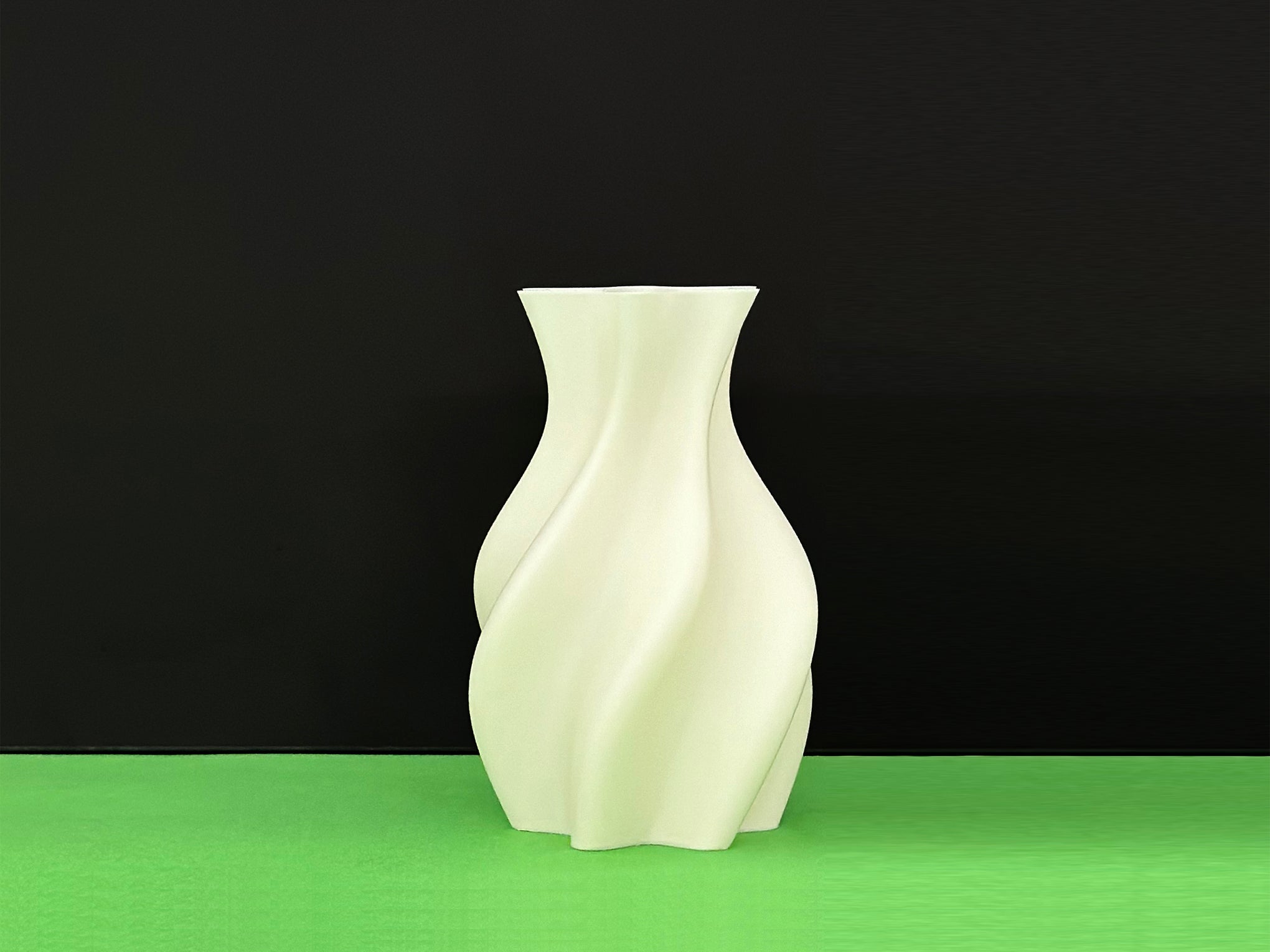
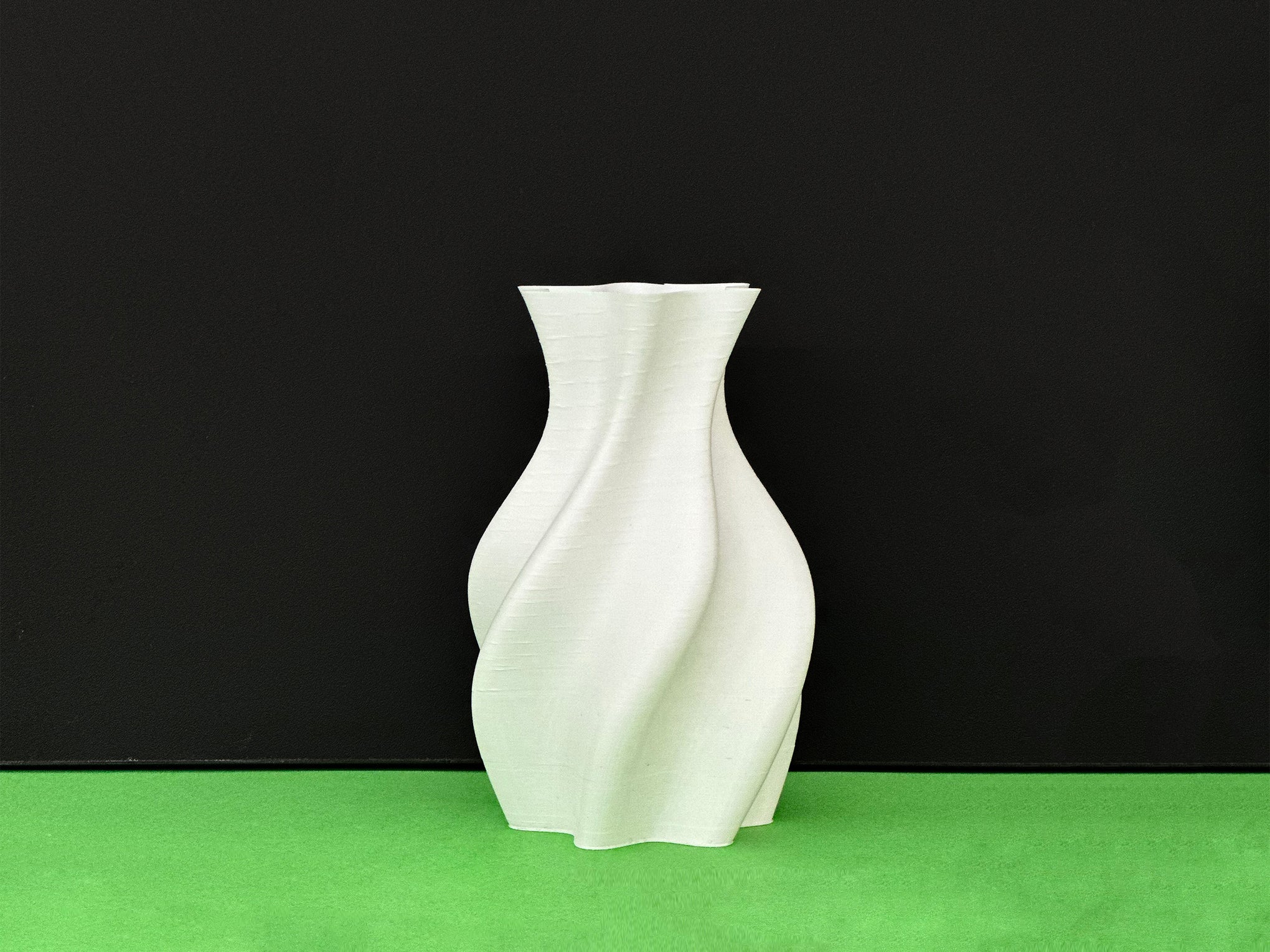
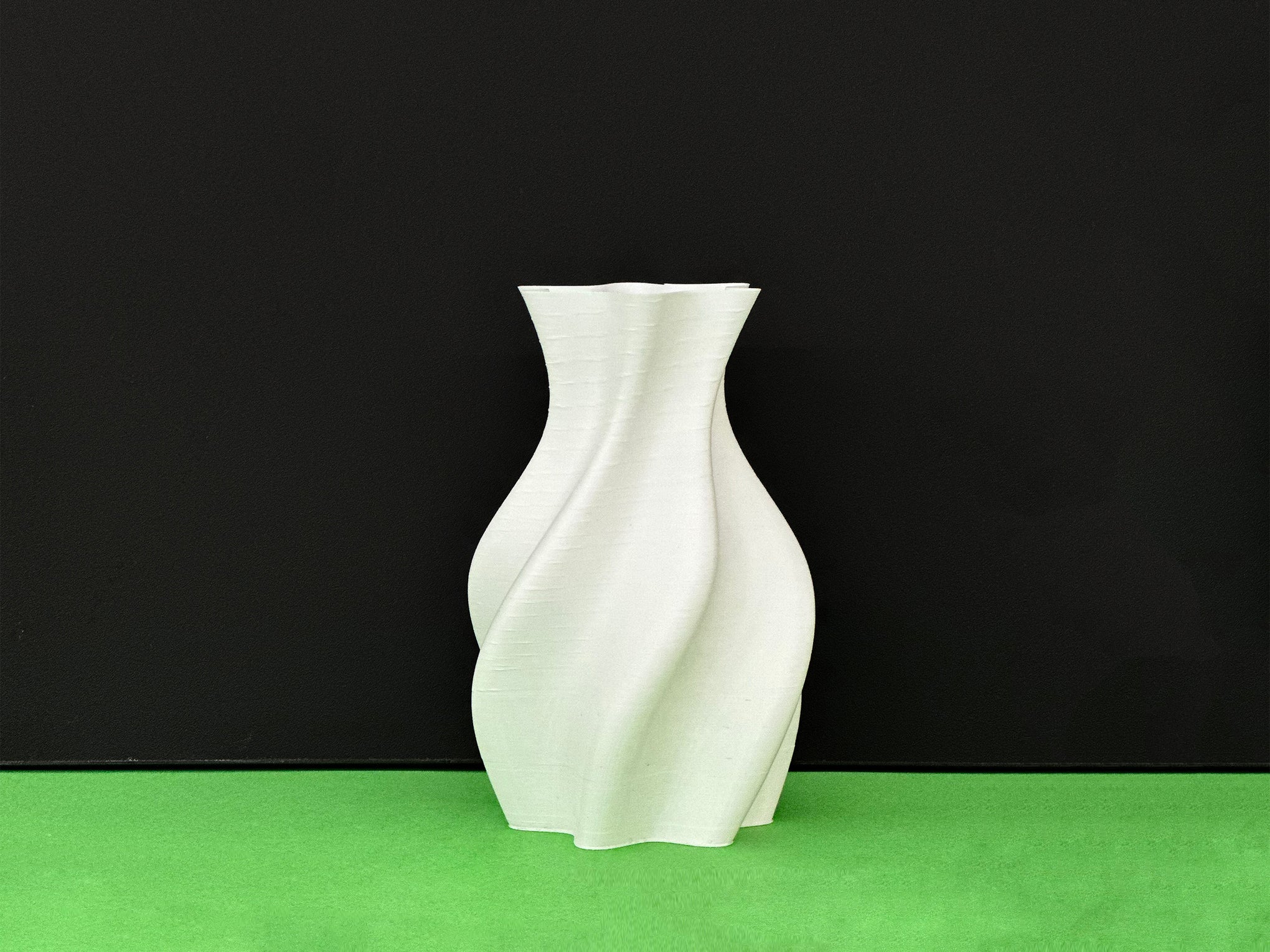